Cedar Grove turns food and yard waste to garden gold
This article was originally published in January 2024
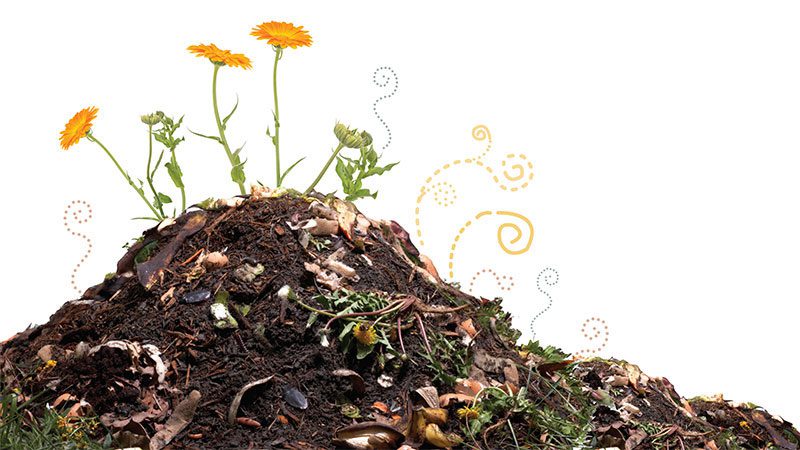
After a visit to Cedar Grove, you might never feel the same about tossing a banana peel in the compost bin with the sticker still attached.
The company’s composting facilities in Everett and Maple Valley are among the largest in the world, processing some 350,000 tons of yard waste and food scraps each year. Through time, air, microbes—and the heat generated by that mix—towering piles of green and brown materials are reborn as around 130,000 cubic yards of rich, dark compost destined for yards and gardens and landscaping. (Some even goes to Sound Sustainable Farms, the vegetable farm founded in Redmond by Cedar Grove. The company donates up to 10 yards of compost annually to schools who are their customers.)
The big compost bins at all PCC stores are processed at Cedar Grove, and its staff worked closely with PCC on sustainability goals such as developing a compostable deli container and sending food waste that’s not fit for human consumption to the composter rather than a landfill.
The 28-acre Everett site opened in 2004 when Cedar Grove began accepting food waste (it started accepting organic materials like yard waste in 1989 in Maple Valley). On a recent tour, workers showed how those scraps go from bins of waste to bags (or truckloads) of soil enrichments.
“Contamination is one of our biggest barriers,” said Sierra Arredondo, the company’s outreach coordinator, speaking near the “tipping building” that’s the destination for incoming deliveries.
“We like to say that our drivers are our first line of defense,” she said. If drivers see compost bins full of black plastic garbage bags holding food scraps, for instance, they’ll reach out to the business “to make sure it’s removed and then assist in any way that we can” to make sure the right materials get in the bin the right way.
A contamination specialist looks at every load, said Jim Simpson, Cedar Grove’s packaging specialist. “He can’t look at every square inch of every load, because we get a lot of tonnage,” but the specialist still finds enough contamination to fill up multiple loads of tall garbage totes every day. A magnetic band pulls out ferrous metal contaminants.
“We get a lot of yard waste, obviously. So we get garden shears, lawnmower blades. (From) restaurants we get forks, knives, stuff like that,” said Gabe Morrelli, the company’s operations manager.
That includes plastic utensils as well as the metal ones, though a new state law taking effect Jan. 1 actually requires compostable utensils to be tinted brown or green, to make it easier (on all sides of the issue) to distinguish compostable materials from non. At that point, Cedar Grove crews will know to pick out the standard white or cream-colored disposable forks and knives from the pile.
“We’re just as good as our material…but we know people aren’t perfect,” Morelli said.
Just a few days earlier, the crew said, along with the usual Hefty bags, aluminum cans, rubber-banded produce and fruit stickers, they found an Everlast punching bag.
Yes, full-size.
Cleared of such contaminants, a ventilation system sucks air out from the tipping building and sends it through a custom biofilter four times per hour to reduce odors. Once screened for foreign material, workers make sure the loads contain the right proportion of green and brown materials—adding wood chips if needed, for instance, if the loads are heavy on summer grasses.
“You can’t make compost grow out of just anything and everything, right? You can have too much carbon, you can have too much nitrogen—you have to have a mix,” said Ryan Dwyer, Cedar Grove’s director of business development and strategic partnerships.
Front loaders then move the piles to a grinder to make sure it’s all broken down in pieces small enough to be exposed to the crucial added ingredients of air and water. Sprayers add that (recycled) water as the material travels to its next stopover, 21 days resting in a heap measuring 164 feet long by 26 feet wide by 10 feet high. The colossal round-edged berms are covered with a specialized breathable fabric to shield them from rain and snow while keeping warm air inside while the composting material heats up as high as 175 to 180 degrees F. (The goal is reaching 131 degrees F for three consecutive days, in order to reduce pathogens.) Computers measure the heat and oxygen content and a fan blows in extra air if needed for microbes to get their work done. “It’s a very high-tech process,” Simpson said, pointing out the probes and wires gathering data from the piles. “You probably wouldn’t think so just walking around it.”
After that first 21 days of decomposition, the compost-in-process moves on to another pile for an additional 14 days of decomposition, then to 14 days in a drying pile to reduce the temperature and moisture content.
Different temperature and timing goals have different purposes, including killing off potential pathogens like salmonella and eliminating weed seeds. Birds are interested in the first fresh loads that come into the plant, seeking out seeds and snacks, but they show no attraction to the later earthy, clean-smelling piles.
A final phase that lasts 12 to 18 months continues the drying and cooldown process, though the pile is still hot and still at work: “You’ve got all those good bugs. Everything’s still working its magic,” Dwyer said. And the long time period allows bits of plastic that weren’t located earlier to become smaller and lighter and more brittle like a Shrinky-Dink toy. A final screening pulls out those dried bits along with blowing out and essentially vacuuming up whatever desiccated fruit labels remain.
Those labels are notoriously difficult to eliminate from compost piles—it’s not the material in the tags that blocks the breakdown so much as the glue.
Material that’s too bulky to make it through that final screening gets pulled out and tossed back in to the first phase. It’s already full of composting microbes and actively breaking down; it acts like an inoculant boost, like yeast to bread dough.
“You gotta take the stickers off,” Simpson said.
It’s satisfying to see the circular nature of the business and to know that the work of sorting out food scraps and lawn trimmings on one end is worth it on the other.
As Dwyer said, “It’s the only solid waste stream that does not have a waste.”
PCC partners
PCC members get a free bag of Cedar Grove Compost with the purchase of any bagged products at participating Cedar Grove facilities.
See details here